Is Tunnel Ventilation Right For Your Dairy?
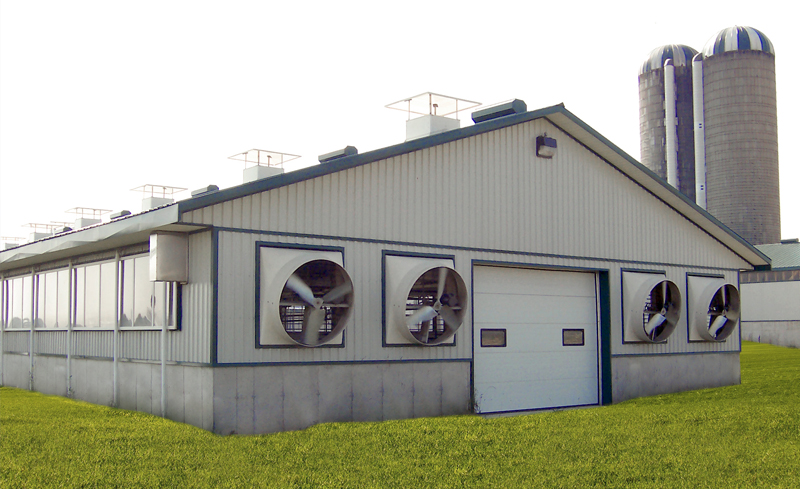
Tunnel ventilation was originally introduced in the 1980s primarily as a solution to address bird mortality issues due to higher bird weights and densities in older, under-ventilated broiler chicken barns. Since these barns were typically 40-feet wide and usually less than 200-feet long with 8-foot high ceilings, they created a natural “tunnel” that was ideally suited to this type of ventilation. One end of the barn was opened for an inlet, while large fans were added to the opposite end. The systems were designed to provide a complete air change every 60 seconds, with an intake air velocity of 350 to 500 feet per minute. This high-speed air moved over the chickens, ruffling feathers, and provided much needed velocity cooling.
Today, we see this same type of system being used in dairy barns for additional high heat ventilation. The typical design of these buildings, however, can create a challenge for this type of ventilation. Structures with widths up to and exceeding 130 feet, lengths exceeding 300 feet, high sidewalls and sloped ceilings combine to create a cross section that most definitely does not resemble a “tunnel”.
To remedy this, some design modifications must be made. In low-profile cross ventilation systems (LPCV), a baffle is dropped down from the ceiling at every stall row to force the air down to cow level, thus ensuring the cows benefit from the velocity cooling. However, this adaptation doesn’t lend itself well to narrower freestall layouts with the air moving end to end, especially if there is a centre drive thru that requires headroom for feeding equipment. In these cases, high-speed circulating fans or cyclone- style fans can be used to boost the air from the inlet end of the building. These fans serve two purposes. First, they keep the air directed down over the cattle so it doesn’t just jet from one end of the barn to the other at a height of 12 to 14 feet from the floor. Second, they maintain a constant air speed in barns measuring 300 to 400 feet in length.
If the high-speed circulating fans are so effective at moving air, are the tunnel ventilation exhaust fans necessary? The tunnel exhaust fans provide the added benefit of rapidly removing both the contaminants and the additional heat being generated by the cows from the barn. A typical system design has enough exhaust capacity to completely exchange the air in the barn every 45 to 60 seconds.
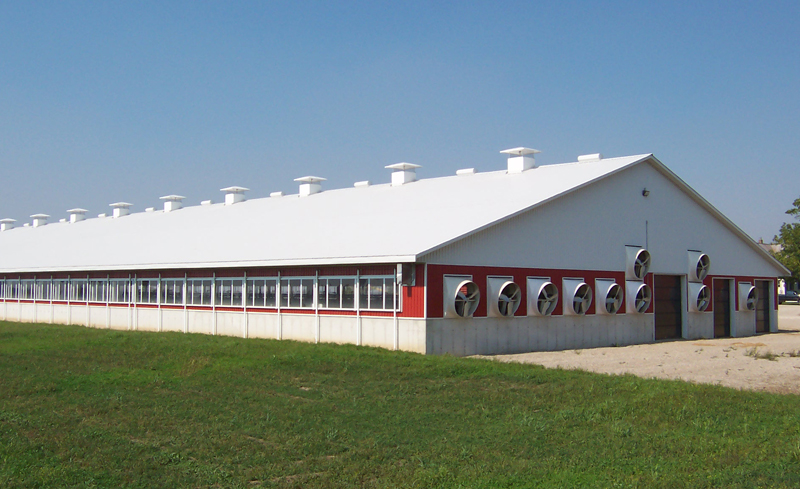
The component that needs to be correctly designed for effective tunnel ventilation is the fresh air intake. The inlet needs to be large enough so the intake air velocity doesn’t exceed 500 to 750 feet per minute. An inlet that is too small produces an intake air speed that is much too fast, which can make it difficult to keep the air flowing at a proper height over the cows. This principle can be demonstrated with a water hose. By squeezing the hose, it not only becomes smaller, but the water speeds up and sprays further. It is still producing the same amount of water, but it is just moving faster because of the smaller hole.
Finally, you need a controller capable of operating all of the individual components in the structure. For instance, as the temperature rises in the barn, the controller will not only turn on your circulating and tunnel ventilation fans, but it will also simultaneously start closing the sidewall curtains. This ensures that in a natural ventilation system, all the air is coming through the tunnel ventilation inlet. All of these steps need to happen in a staged manner so the amount of tunnel ventilation increases as the building temperature continues to rise. The inlet also needs to be opened in conjunction with the fans so the size of the opening always matches the number of exhaust fans running, which will keep the air speed constant. There will also be times where the tunnel system is needed during the day, but natural ventilation will be required overnight. In this situation, the controller needs to switch back and forth from one system to the other.
With so many changes and adjustments required to keeping your ventilation system operating at optimal performance, it is of critical importance to have a controller that has the capability of handling it all.
Tunnel ventilation may not be a perfect fit for every dairy facility, and if not properly designed, this system could end up costing you a lot of money on fans and hydro with no real benefit. However, if designed and managed correctly, tunnel ventilation can provide your cattle with added comfort in the hottest of weather and ultimately contribute to a healthier bottom line for you.
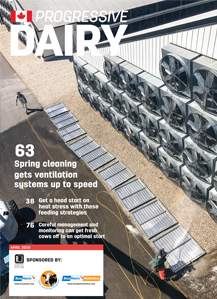
As seen in Apr 2020 edition of Progressive Dairy Canada.