Natural Ventilation Technology Choices for your Dairy
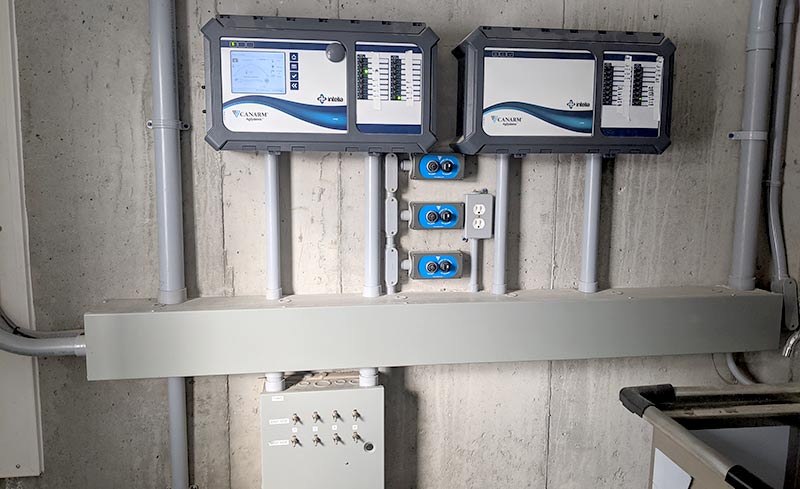
Over the years natural ventilation has lagged behind with regards to control technology. This is mainly due to the fact that, unlike mechanical ventilation, which requires a controller to adjust power levels or turn fans and inlets on and off, natural ventilation curtains or panels can be operated with a simple hand crank. The simplicity of this sytstem was appealing both from an initial investment and an operating cost point of view.
As more and more dairy facilities were constructed to house cattle year-round, the need to improve control of the interior temperatures became more important. This was not easily accomplished with manually operated sidewalls - especially in the spring and fall when large fluctuations in temperatures over a 24 hour period tend to occur. This led to more systems being equipped with electrical drive units and thermostat controls that would automatically open and close the sidewalls to maintain a desired interior temperature that was recorded by remote mounted sensors.
Fast forward to today, where our society is technology-driven with advancements arriving seemingly every day. In my 40 plus years of experience, I have seen the largest increase in technology during my lifetime than any generation before. As is the case with many other sectors the same can also be said for the dairy industry.
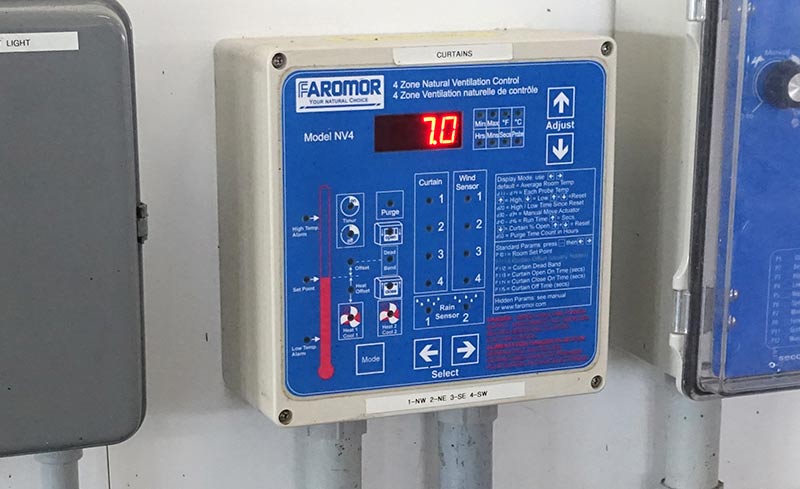
Today, we see dairy operators wanting to have more and more systems within their facilities running automatically - from robotic milking, robotic feeding, automatic manure systems, controlled lighting and more. This has led to the design of ventilation control systems with the added capacity to integrate other operations into one controller. The common functions include control of complete ventilation and additional summer ventilation systems with both on/off and variable speed, timed sprinkler systems and on/off/dimmable lighting with light intensity sensors to maintain a constant light level in the barn 24 hours a day. In addition to increased control functions, these new generation controllers also use additional input measurements to assist in ventilation adjustment, such as outside temperature, inside and outside humidity, ammonia and CO2 levels along with wind speed, direction and rain sensors.
The other area of increased interest for dairy farmers is the ability to collect data and to monitor and adjust the control system from a remote location using either a PC or a smartphone. These systems can also be used to detect and alert the operator of any alarm conditions occurring within the facility. Caution should be used however, since you are never certain what other effects a change in control setting may cause.
While there is a large amount of high-level technology now readily available, it does come with increased cost. Someone once told me that the only limitation to the amount of technology you can obtain is the size of your budget. The key to getting the right system for your barn is to evaluate what features you need to improve the current environment. Your ultimate goals should be healthier cattle, a reduction in operating costs (leading to improved profitability) and automatic functions that will assist with your workload. I always caution people when in these types of discussions to be wary of the “bells and whistles” that may look fancy but yet do nothing to meet the above-mentioned goals.
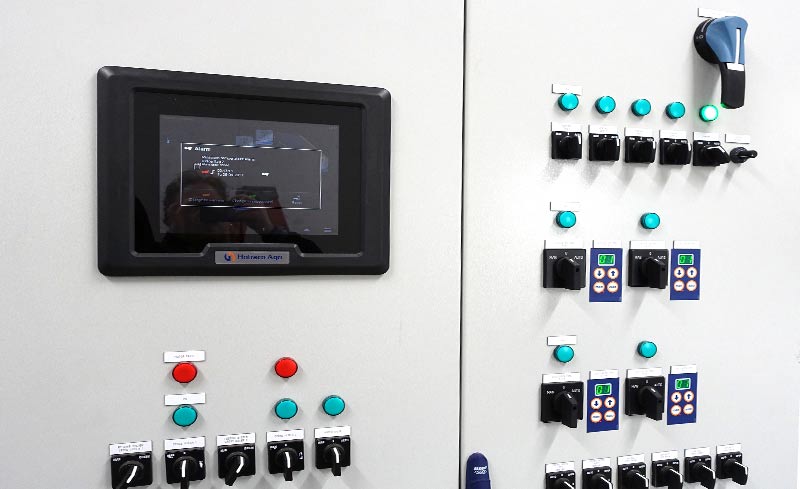
The other key factor to consider when deciding on which system is best for you is your level of comfort with the company you are working with. The downside of having several different functions controlled by one system is that if it goes down, all of the individual operations it is responsible for in your dairy may no longer work. Having parts readily available and 24 hour service are a must with these types of advanced control systems. When using these type of controllers, it is also imperative that you have proper electrical surge protection for both your power and control signal wiring. An electrical surge from nearby lightning or from the main power grid can cause thousands of dollars in damage in an instant and leave your facility non-functional.
As always, I recommend that you meet with a ventilation professional during the planning stages for your new dairy to review and design the ventilation control system that is best for your barn. This is an investment for both you and your cows for many years to come so make sure you make an informed decision.
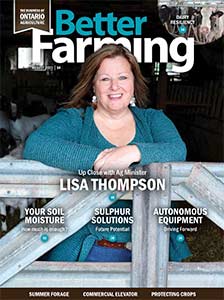
As seen in Aug 2021 edition of Better Farming.